Project leader:Jianghan Shen |
Contacts:Xing Wei |
Tel:86649777-6618 |
Email:satellite@syn.ac.cn |
1. DMTO & DMTO-II Technology Overview
1.1Technology Overview
The methanol to olefinstechnology refers to a process of converting methanol and/or dimethyl ether as raw material to light olefins by a fluidized catalyticconversion system. Our patent proprietary technology shall hereinafter be referred to as “DMTO technology”. Olefin recovery technology refers to a process of separating light olefins to predominantly polymer grade ethylene and polymer grade propylene and otherby-products.
1.2 Process Introduction
The DMTO methanol-to-olefins technology(DMTO&DMTO-II) is licensed worldwide by SYN(Syn Energy TechnologyCo., Ltd.) and LPEC(Sinopec Luoyang Engineering Co., Ltd). This breakthrough technology enables licensees to produce olefins from methanol, an economical alternative to cracking crude-oil-derived feedstock. The process provides enhanced olefins yields.
The DMTO process converts methanol to light olefins – predominantly propylene and ethylene. The process is noted for its high methanol conversion and olefin selectivity, low investment cost, and low energy consumption.
Process Features |
Client Benefits |
Dense-phase, circulating fluidized reactor |
Low pressure drop; Uniform bed temperature distribution; Adjustable propylene-to-ethylene (P/E) ratio |
High activity catalyst |
High olefins yield with high selectivity to propylene and ethylene; Low catalyst-to-methanol ratio |
Low energy consumption |
Specific energy is 55% compared to naphtha cracking |
lPerformance Characteristics
The reaction takes place in an FCC-type, dense-phase, circulating, fluidized-bed reaction system with continuous catalyst regeneration. The reaction is highly exothermic, and the fluidized bed improves removal of excess heat, enabling uniform bed temperature distribution. Tuning the operating conditions of the reactor and the regenerator allows the P/E ratio to be adjusted. The catalyst is a molecular sieve acid catalyst and its high selectivity to light olefins is the result of both the activity of the acid sites and the favorable pore diameter of the molecular sieve framework structure.
lProcess Flow Diagrams
Reactor Section
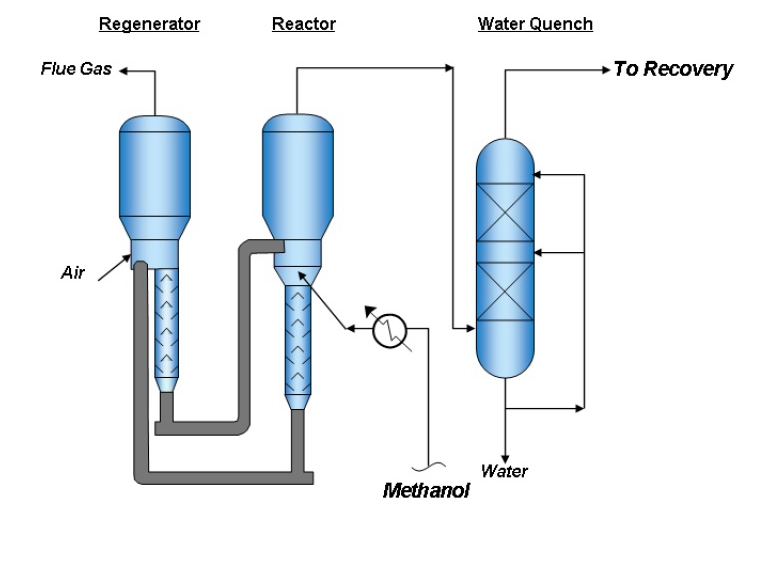
lProcess Description
Methanol and water are preheated and fed to the fluidized-bed reactor and contacted withcatalyst in the reaction zone at temperatures between 400 and 550°C.Part of the fluidized catalyst from the reaction zone continuously circulates in a closed loopbetween the reaction system and the catalyst regeneration system, where coke is removed fromthe catalyst.The reacted gas is cooled by interchange with the feed gas and by direct-contact with circulatingwater. Water formed during the reaction is condensed.Both reaction and catalyst regeneration are strongly exothermic. Heat integration is applied toimprove energy efficiency.
1.3Technology Advantage
Dalian Institute of Chemical Physics (DICP) of the Chinese Academy of Sciences (CAS) is a well-known R&D center in chemistry and chemical engineering, and is acknowledged worldwide as a leader in the development of MTO technology. DICP has been engaged in continuous MTO R&D for more than 30 years with the sufficient support of theoretical foundation. From the early of 1980’s, DICP commenced to research and develop Methanol and DME to Olefins Reaction, and the pilot test in fixed bed and the fluidized bed were sequent completed. Moreover, DICP firstly reported the experiment results of application of SAPO-34 molecular sieve catalysts in MTO reaction in the world. Based on the advanced technology, DICP cooperated with SYN and LPEC to establish the first worldwide 16.7kta MTO demonstration plant and finished the test with exciting performance in August 2006. The demonstration plant, which is the unique unit worldwide for MTO process, has run successfully and made great achievements and won the national appraisal.
The first commercial application for DMTO technology is to the plant of the Shenhua Baotou Coal Chemicals Co., Ltd. in Baotou, China, which has been in steady commercial runningmore than 10 years. The plant is designed to produce 600KTA of ethylene and propylene from 1.8 million tons of methanol per year. This plant is the first commercial MTO plant in the world, which marks a significant milestone for MTO technology commercialization in the world.
MTO unit composes MTO reaction section and light olefin recovery section. For MTO reaction section, MTO technology is adopted. Currently there are three kinds of MTO technology licensed by three different licensors, including DICP-DMTO(here DICP-DMTO includes DMTO and DMTO-II, 26 contract plants with olefin capacity of 15.25 million ton/a), UOP/Hydro-MTO(8 contract plants with olefin capacity of 3.52 million ton/a), and Sinopec-MTO(5 contract plants with olefin capacity of 3.47 million ton/a). The contract plant number and total olefin capacity of each licensor are listed in Table 1.1.
Table 1.1 Contract plant number and total olefin capacity of different licensor
Licensor |
DICP-DMTO |
UOP/Hydro-MTO |
Sinopec-MTO |
Contract Plant Number |
26 |
8 |
5 |
Total Olefin Capacity(million ton/a) |
15.25 |
3.52 |
3.47 |
Market Share(based on olefin capacity) |
68.6 % |
15.8% |
15.6% |
In order to increaseethylene and propylene yield,MTO plants could further convert C4+ byproducts to ethylene and propylene via technologies such as DICP-C4+cracking/Total-OCP/Sinopec-OCC/Lummus-OCT.DMTO-II technologyis able to achieve MTO reaction andC4+cracking processat the same time with the same catalysts, which ismore efficientand reduce10% methanolconsumption forone metric ton olefinsproduction.
China has the most MTO commercial plants(totally 26 plants) on operation, including 16 DICP-DMTO plants(here DICP-DMTO includes DMTO and DMTO-II) with total olefin capacity of 8.36 million tons/a, 6 UOP/Total-MTO plants with total olefin capacity of 2.92 million tons/a, 3 Sinopec-MTO plant with olefin capacity of 2.27 million tons/a. DMTO is the most advanced and mature MTO technology in the world with the biggest market share of contract plants(68.6% based on olefin capacity), as well as the total olefin production capacity of on-steam MTO plants(61.7%). The on-operating commercial MTO plants number and olefin capacity of different licensor (up to March. 2021) in Table1.2.
Table 1.2 On-operating Commercial MTO plants number and olefin capacity of different licensor (up to March.2021)
Licensor |
DICP-DMTO |
UOP/Hydro-MTO |
Sinopec-MTO |
Commercial MTO plants number |
16 |
6 |
3 |
Total olefin capacity(million ton/a) |
9.3 |
2.92 |
2.27 |
Market Share |
61.7% |
21.5% |
16.8% |
In summary, DICP-DMTO is in the leading position in terms of contract plants as well as on-operating commercial plants. DICP-DMTO process has become the most advanced, mature and reliable MTO process in the global market.
Besides, in MTO technology R&D history, DICP-DMTO technology keeps in the leading position in the world. DICP has been engaged in continuous MTO R&D for more than 30 years with the sufficient support of theoretical foundation. From the early of 1980’s, DICP commenced to research and develop Methanol and DME to Olefins Reaction, and the pilot test in fixed bed and the fluidized bed were sequent completed. Moreover, DICP firstly reported the experiment results of application of SAPO-34 molecular sieve catalysts in MTO reaction in the world. Based on the advanced technology, DICP cooperated with SYN energy technology Co., Ltd and Luoyang Petrochemical Engineering Company, Sinopec to establish the first worldwide 50 ton/day(methanol) MTO demonstration plant and start the demo test in 2004. The demonstration plant, which is the unique unit worldwide for MTO process, has run successfully and made great achievements and won the national appraisal. For the second generation DMTO technology (DMTO-II), its demonstration test successfully completed in June 2010 and won the national appraisal. While UOP/Hydro’s MTO pilot plant in Norway completed the pilot test with 0.75 ton/day(methanol) capacity in 1995. UOP/Total’s MTO demonstration plant in Belgium started the demo test with smaller capacity 10 ton/day(methanol) in 2009.
2. Technology Progress
2.1DMTO demonstration
In 2004, thefirstDMTO demonstration plantin the world with a capacity of16.7KTA methanol feedstockwasstartedupinChina.Experiences from the demonstration plant are as followed:
1) The conception for scale up design of MTO unit was demonstrated, which validated the principles of DMTO process and engineering technology.
2)The special DMTO catalyst was produced in large quantity and the excellent propertiesof the catalyst weredemonstrated.
3) Quality standard of methanol feed was established and tested.
4) Basic data for PDP design of large MTO commercial plant was obtained,which establishesa foundation for design and operation of a large DMTO commercial plant.
5) Startup, operation and shut down experience
6) Further understanding of the effect of reaction variables (temperature, space velocity, coking, circulation rate, resident time, etc.) on large unit.
7)The comparability between pilot test and demonstration test of MTO was analyzed, whichhasproved that MTO demonstration test and experienceare indispensablefor the design oflarge commercial plant.
8) The experience from DMTO demonstration enables us to deeply analyze the critical problemfor thedesign of large commercial plant, and to optimize the design.
9) The design of large commercial plant (Shenhua Baotou MTO unit of 1800KTA methanol feedstock) has already been finished based on the demonstration test experience. Other design objectives are expected to achieve the target.
2.2 DMTO-II demonstration
Based on DMTO demonstration, DMTO-II technology was developed. In June2010, DMTO-II demonstration test passed the national appraisal.DMTO-II is an integrated technology of DMTO reaction with the technology of converting DMTO by-products to objective olefins (C4+ cracking process for short) using by one catalyst and taking the advantage of heat integration of exothermic feature of MTO main reaction and coke combustion (in the regeneration reactor) with endothermic feature of C4 plus cracking reaction in the same unit. DMTO-II enables the yield of ethylene and propylene to be dramatically increased and the e the P/E ratio to be adjusted more widely, as well as the energy consumption and the cost to be decreased. DMTO-II will decrease the methanol consumption to 2.6~2.7 per metric ton of olefin.
2.3Industrial Utilization
DMTO and DMTO-II have completed industrial domotest, and become a mature process utilized in commercial industrial complex widely and successfully in recent years.
3. Commercial License
3.1 Licensor
SYN Energy Technology Co., Ltd (SYN) is a joint venture company contributed by Dalian Institute of Chemical Physics, Chinese Academy of Sciences (DICP), Shaanxi Coal and Chemical Industry Group Co., Ltd. and Chia Tai Energy Chemical Group Limited, and controlled by DICP.
DICP is one of institutes of Chinese Academy of Sciences (CAS) founded in March, 1949. It is a multidisciplinary institute engaged in both fundamental and applied researches of chemistry and chemical engineering, especially with strong abilities for technological R&D and mainly undertakes national and industrial key projects. The R&D researches on catalysis and chemical engineering of DICP have won a great reputation worldwide.
DICP began MTO research and development in the early of 1980s and is the first in the world to report the application of SAPO-34 molecular sieve catalysts for MTO reaction.
Luoyang Petrochemical Engineering Corporation, SINOPEC (LPEC)is the partner of SYN. It’s founded in 1956 and is a leading engineering firm under SINOPEC. It has state Class A qualifications for project engineering and project implementation. As a pioneer of Fluidized Catalytic Cracking (FCC) technology in China, LPEC has led the development of FCC technology in China for more than forty years and been at the leading edge in the world since the first FCC unit successful designed by LPEC had been operated in 1965.
LPEC is very strong and extensively experienced in the development of engineering technology of fluidized-bed reaction- regeneration process and has successfully engineered over 60% of FCC units in China.
3.2 Reference Plants
The DMTO processwasstarted license sincetheyear 2008, and 26 license contracts has been signed up to now for a total planned and operating olefin capacity of 15.25 MMTA.The Shenhua Baotou DMTO plant, the first of these, successfully started up in August 2010, and has been run continuously for a dozen years. A second operating commercial facility using the DMTO technology, Fund Energy (Ningbo) DMTO, was successfully started up in Jan. 2013. The year 2014 is a peak year of DMTO plant startup, totally 5 plants have been successfully started up and on operation, including Yanchang Petroleum Group (Jingbian), China Coal (Yulin), Baofeng Energy (Ningxia), Shenda Chemicals (Shandong), PCEC (Pucheng)(DMTO II). In the year 2015, Zhejiang Xingxing(Jiaxing) DMTO plant and Shenhua(Yulin) DMTO plant started up. In the year 2016, ChinacoalMengda(Inner mongolia) DMTO plant, Qinghai Salt Lake(Golmud) DMTO plant and Fund Energy (Changzhou) DMTO plant started up. In the year 2018,Shaanxi Yanchang Petroleum Group(Yan’an) DMTO plant started up. In the year 2019, Baofeng Energy (Ningxia)-Phase II DMTO plant started up. In the year 2020, Yanchang Petroleum Group (Jingbian)-Phase II started up.The total capacity of olefins from the 16 DMTO plants on operation has reached 9.3 MMTA, which drive the rapid formation of methanol to olefins strategic emerging industry in China.